CAQ-Software at Continental: Quality Ensures Driver Safety
Those active in the automotive manufacturing sector must be able to compute. Alfred Teves’s company must have agreed with this statement when it took over the production facility Friden-Singer in 1971. Up to this point the company, located in the Flemish region of Mechelen near Brussels, engaged in manufacturing mechanical adding machines. These machines possessed an especially impressive and highly precise interior structure.
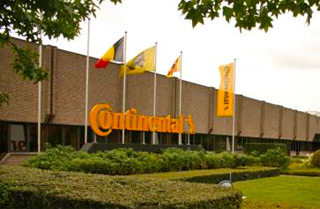
Due to Japanese innovations in electronic calculators, the company’s future and that of its then 360 employees appeared in jeopardy. This was to represent the basis for an impending reorganization. To this day, the employees at this Belgian company are specialists in the area of mechanics, but the company’s business focus has changed dramatically. Continental Teves GmbH & Co. KG manufactures singular components for highly complex anti-block brake systems in the automotive industry. What began in the 1980s with the manufacturing of individual valves, valve blocks, and sensors for the so-called ABS system has continued to develop over the years into the manufacturing of complete systems.
If one enters the production areas of the company, taken over by Continental AG in 1998, one hears highly technical acronyms everywhere. Although the acronyms ABS, ASR, and ESC are familiar to most knowledgeable automobile drivers today, at Continental the terms FSA, AYC, EBD, RBS or HSA are just as commonly used. This gives the impression that developments which have created these systems already belong to the serial production standard of a common automobile.
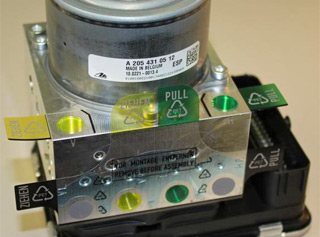
In fact, these strange sounding acronyms, most likely unfamiliar to the layperson, are indeed part of everyday production at Continental. As one of the largest manufacturers of ABS/ESC systems, with a market share of ca. 40%, and 400 km off from its Frankfurt headquarters, the company develops and produces 130 million valves for the automotive industry. This means that, at 10 valves for ABS and ESC per automobile, Continental produces components for 13 million automobiles in Europe per year. It is a matter of course for Continental that, in order to reach such high production quantities – which are impressive even in the area of complete manufacturing of ESC and ABS-systems – an almost entirely automated manufacturing process is needed. In 1999 the company celebrated the production of the 150 millionth component, manufactured in the preceding 15 years, but only two years later valve production had increased to a total of 100 million more – and in June 2009 the production of the one billionth valve was celebrated.
In addition, the company produces over 26 million wheel speed sensors per year. These monitor the speed of each individual wheel of the car. The information they gather is used to prevent the wheels from locking and determine when the wheels are spinning, taking appropriate control action to maintain the vehicle’s stability and steering responses.
Quality in the Automotive Business
The basis for such an impressive production achievement includes, beyond custom development of highly specialized and custom-made production machines, the keeping to strict quality standards. “In the automotive industry there is no tolerance level for imperfection”, the head of the quality department, Bart Ceulemans, explains. “If we do not work 100% error-free our products would constitute a risk to a car drivers’ wellbeing. No one in our line of work would be willing to take a chance on something that important”.
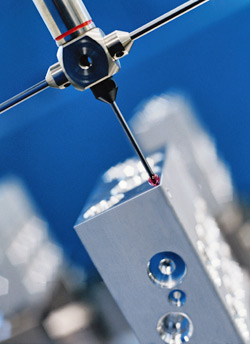
But since making errors is only human, Continental depends on precise computer technology. Since 1994, the company uses the superior abilities and high performance of CAQ AG Factory Systems in Rheinböllen. Quality expert Ceulemans was the man in charge of implementing the CAQ software at the time.
According to Mr. Ceulemans, his company never regretted making this decision in the early nineties. The CAQ software was custom developed to meet the special demands of this Belgian production company. During the development phase, Continental was able to voice software program preferences and desires which were eventually incorporated into the programming of the final version of the software Compact.Net. The performance of the software is convincing: “We know, that the software system can do even more, but with the licenses which we have required so far, including the expansion software modules, our production is able to achieve the highest possible degree of quality”.
Even though Continental utilizes a relatively small number of licenses of the base module Compact.Net, the company is always ready to read and control its acquired data since licensing agreements only refer to simultaneous system access and not, as is the case for most other software vendors, to number of installations. To this extent, it is possible to control and retain strict quality requirements at over 30 workstations with the support of the quality assurance system.

In order to adjust the software’s capabilities to perfectly fit the demands of the Belgian company, the complementary modules for gauge management PMM.Net, failure modes and effects analysis Risk.Net, as well as the form generator Form.Net were integrated into the overall system. The possibilities of FMEA impressed the customers of the brake manufacturing company the most.
Compact.Net allows Continental to provide each of its customers with an appropriate APQP/PPAP report that documents the faultlessness of an entire production batch without the need for any paper. In the past couple of years, Compact.Net was supplemented with the expansions APE.Net and Mail.Net. These optional programs facilitate the automatic import of measurement values – such as 3D-meaurements – from measurement protocols directly into Compact.Net. If a process violation should occur, the person responsible for quality assurance in the company is automatically informed via e-mail.
Additional Links