CAQ-Software at Rockwell Automation: Quality Through Precision
When one speaks of Switzerland, the first things that come to mind are great cheese, powerful banks, and a multilingual society. Most of all, however, it was the precision work of watch and clock manufacturing that made the Land of the Confederates famous.
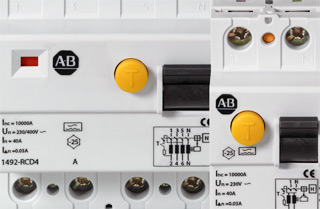
Although clocks may tick differently today in this country (which is divided into Cantons) than in years past, and timepieces now only account for a small portion of the Swiss GDP, it is still the concept of precision work which defines both the high-value transformations in the country as well as the efficiency with which it is closely associated.
Guided Quality
At the Aarau-based firm Rockwell Automation, the most important principle is unmatched precision and the quality that comes with it. Besides the production of time measuring devices, Rockwell’s specialists perform precision work on components for electromagnetic control devices (EMCDs). The parts produced in the canton of Aargau are used in a range of sectors: this subsidiary of the globally-operating American corporation is active in both the automotive industry as well as in timber and metal conversion, and its client portfolio includes not only companies from consumer goods sectors, but also firms involved in petroleum, chemicals, and pharmaceuticals, not to mention the semi-conductor industry.
Generally speaking, Rockwell operates where the individual control systems of electro-mechanical devices can be profitably deployed for the manufacture of high-value products, and where consistent high quality is an important factor in daily production. One requirement for the production support that Rockwell provides is its own adherence to strict quality standards, which derive not only from the requirements of the customer, but also from requirements related to certifications. In order to satisfy these demands for quality, the firm has relied since the start of the millennium upon computer-assisted quality control through the software Compact.Net, which was fine-tuned to meet individual requirements of this Swiss company.
Individualized Standard
While searching for appropriate software to evaluate the measuring devices already on hand, the former manager of production planning at Rockwell Automation came across the software solutions offered by CAQ AG Factory Systems. In-depth conversations with the software provider, along with test-runs of the software in actual production on location, convinced the decision maker to employ the system in its entire Quality Control Department.

Today a single module of the CAQ system, PMM.Net, manages over 4,000 pieces of test equipment. Currently there are 55 users (and growing) who operate the terminals in the Production, Industrialization, and Quality Control departments. In addition to the core software Compact.Net, the system has been expanded with other modules in order to achieve an optimized customization of the standard software: APE.Net for the automatic inspection data gathering of protocol-ready testing and measuring machines, Form.Net, a graphic form generator, and PMM.Net, a gauge management system with MSA. The previously used system, IBM ZOS 390, was able to be integrated optimally into the system through both the module Connect.Net as well as the interface which this module made possible, so that today production batches of up to 300,000 pieces can be comprehensively monitored, controlled, and evaluated.
Flexible Enhancement
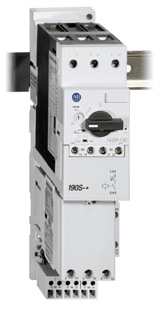
The possibility for customization of the standard software offered by CAQ AG Factory Systems is also something that time and again convinces Heinz Lurati, who is in charge of CAQ software implementation, that “his” software solution is indeed the best. “The system adapts itself optimally to the requirements of our organization. Soon we will be reviewing the integration of our Czech production center. With the new CAQ.Net release, available since the beginning of 2006, even our suppliers will be able to use our test plans, while there is the possibility to collect the corresponding data automatically in our system and further work with that data here in Aarau. That kind of adaptability – even in running processes – is, as far as we know, only otherwise available in individually developed software solutions, whose costs would far surpass the current magnitude we have with CAQ AG Factory Systems.”
“This kind of adaptability is made possible by the openness of the system, which in our opinion is an important criterion of success for this excellent software,” continues Marcel Schönholzer, who as the group manager of parts planning in the Industrialization Department is, like Mr. Lurati, responsible for the CAQ software.
“The interface with our IBM ZOS 390 was just one of the many possibilities used by CAQ AG Factory Systems to prove the flexibility of the system. Even while the system is online, we continually receive new developments from the programmers that help us to work with the system even better and to handle assignments more easily. In this way, we are continually provided, in the form of regular updates, with enhancements that not only address our own desires, but also those of the other users. Just as in open-source systems, the system is continually expanded with new optimizations which set the software apart from that of potential competitors.”
In order to become acquainted with the new features and improvements made by the programmers, Mr. Lurati regularly attends the training sessions offered by the software provider CAQ AG Factory Systems. Following these sessions, he then schools the appropriate inspectors in new ways to implement the software.
Even new employees, who as workers in the production shops previously had no access to software applications, are trained by Mr. Lurati. The incremental workload which this entails amounts to no more than a single workday, according to Lurati, due to both the logical structure of the program as well as the coherent, Windows-style user interface, which is sufficiently self-explanatory that even workers with little experience with a PC are able to master the necessary steps in the shortest amount of time. Mr. Lurati and Mr. Schönholzer see 4,118 testing devices, 55 users, and applications in geographically distant production facilities as just one step along a common, successful path of cooperation with CAQ AG Factory Systems. Thus we can anxiously await the continuation of this exciting success story …
Additional Links