CAQ-Software at Vosseler: Cold-Pressed Quality
At Vosseler GmbH in Aldingen, compression moulding is one of the most important jobs. The company, steeped in tradition since 1948, processes wire of up to 35 mm, in order to manufacture cold-formed parts. Every day, batch lots of up to two million pieces leave the factory, including locking screws, coupling nuts, as well as specialized aluminium and steel parts for the automobile industry, their suppliers, and the engineering industry in general. In order to manufacture locking screws and other parts with even greater width across flats, the company also employs warm as well as cold formed molding blanks.

Products used for hydraulics and the automotive industry, which are part of the manufacturers main areas of focus, require an extraordinary fitting accuracy in order to guarantee the required thicknesses. Tolerances which at times are less than 0.05 mm at production speeds of up to 150 pieces per minute place extremely high demands on tools and machines. This mid-size company has depended on the support of CAQ AG Factory Systems since 1999 in order to guarantee this kind of performance. Vosseler GmbH is QMS certified, satisfying the demands of the DIN EN ISO 9001:2008 and of the ISO/TS 16949:2009 standards.
Qualitative Collaboration
It was an obvious decision for the quality control manager to choose qualitative collaboration with the globally operating quality assurance software provider CAQ AG. He based his decision on pre-existing contacts and his knowledge of the modular system structure.
“The ‘data collection system’ that we used until 1999 simply did not measure up to our need for systematic evaluations and analyses of data, and considering the upcoming turn of the millennium, it was clearly the right time to switch,” the quality control manager explains. IT-expert Christian Meng, who is likewise responsible for the implementation of the CAQ software adds,
“Naturally we had a look at the solutions proposed by other vendors in order to check out what was being offered in terms of performance, integration, and support. This comparison ultimately confirmed the conviction that we had indeed found the perfect partner in CAQ AG Factory Systems.”
Modularity
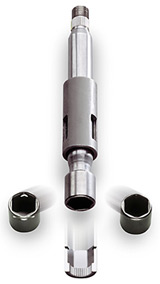
In light of the likely growth of the company as well as a possible increase in the number of production facilities, special attention was paid to the expandability of the future quality control system. CAQ AG factory systems with Compact.Net offered the best possibilities: While the core software already covers the bases of modern quality and process management, from receiving to the production process to the shipping of the final product, supplementary modules can be individually added depending upon customer needs.
This potential for customization was also put to use by Vosseler after an initial adjustment period. In order to provide paper-free quality reports to the customers for their respective products, and in order to visually fit these reports into the format desired by the respective customer, it was decided within a very short time period to expand the system to incorporate the modules Mail.Net and Form.Net. The system was also expanded with the module for gauge management, called PMM.Net, which made managing measuring devices possible. The module for complaint and service management REM.Net was also incorporated into the existing system structure in 2004. Except for gaining additional performance features, no additional training was necessary in order to continue working successfully with the already familiar user interface.
Individual Application
In order to best utilize the system’s possibilities, direct access to the software is given not only to the 5-person quality management team, which is primarily responsible for inspection planning as well as control and results reporting to both management and customers, but also to the individual workers themselves.
The cooperation between production and quality control is now accomplished completely without paper. The employees log on to the system and receive the current inspection plan to work on, which is continually updated with the latest data and graphics. In this way everyone is on the same page, ensuring that quality reporting is both consistent and timely.
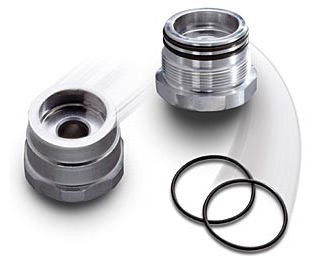
The incorporation of production line workers into the system, which was introduced by Vosseler in order to increase work-flow, was made possible by filtering options developed by CAQ AG Factory Systems. While quality control personnel have the option of accessing and compiling data from all areas of the system, individual workers have appropriately restricted access through their own logins, which eases the process through special means and standardized procedures.
“Through this simplified presentation we don’t even need separate training in order to familiarize our production workers with the system,” says IT-specialist and system administrator Christian Meng excitedly, who, by means of the Top-Service-Package, regularly makes use of the training provided by CAQ AG Factory Systems in order to independently train his own workers in the latest practices. Since such a procedure also guarantees an optimal cost-benefit ratio, which is important to top management, the employees in quality control are sure that the decision to employ what has become “their software” was indeed the right one.
Additional Links